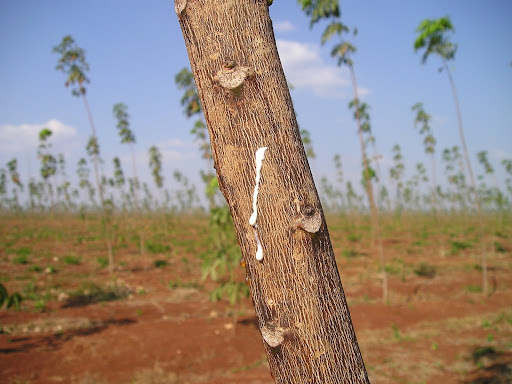
From the pink eraser at the end of your pencil to the black tires that make your car spin, rubber parts seem to span the entirety of the rainbow. But the blue surgical gloves your doctor uses at your checkup or the red latex pants your mom refuses to get rid of were not made from blue or red rubber trees.
Instead, that rubber was harvested from rubber trees and colored artificially by manufacturers depending on the end user’s specifications. Coloring rubber correctly requires a knowledge of chemistry and patience to create just the right shade. And while some rubber parts are colored for specific reasons, we can all agree sometimes a purple rubber gasket is just more fun than a plain white one.
What color is natural rubber?
Natural rubber is harvested from rubber trees, processed and shipped worldwide. Before processing, natural rubber exits the tree in the form of a white, milky latex.
Unless the latex is contaminated, that means the natural color of rubber straight from the tree is white. Natural rubber that does not undergo any sort of specific process will theoretically remain white through the curing process.
Synthetic rubbers, on the other hand, which are made artificially and do not occur naturally, vary in color depending on how they are made. Rubbers with more beta carotene will be more amber in color or have an orange hue. Some synthetic rubbers are formulated with natural rubber and maintain their milky white shade.
What is the most common rubber color?
After Charles Goodyear first vulcanized rubber in the 1840s, it took another decade until scientists invented synthetic rubbers in World War II because rubber trees were commonly found in or near Axis-occupied countries. From there, innovation took hold as chemists invented new types of rubbers and began to create rubber colored with specific additives and pigments.
Today, the most common rubber color is black because carbon black is the most popular rubber additive. Carbon black improves physical and chemical properties, and its coloring is so strong that the tiniest bit will turn an entire part black. It’s a very efficient, low-cost way to color rubber and is consequently very popular.
Is it harder to work with colored rubber?
Outside of carbon black, rubber colors are made by adding pigments to adjust coloring. Rubber molding companies like Custom Rubber Corp. can make any color you can imagine. This rubber is not harder to work with than uncolored rubber, but it can add cost depending on the color you select.
While carbon black is a cheap and abundant additive, purple pigments are a few cents more per pound. Additionally, injection molding machines mainly run black, so it can cost more if the manufacturer has to clean out the machine before running your purple parts. It’s expensive to clean and change out injection molding machines to get all that black out, but it’s still often the fastest option.
If time is not of the essence, you can save money on colored rubber parts by using a compression or transfer mold. Cycle times will be longer with a bit more waste, but you’re guaranteed solid purple parts without the cost or hassle of cleaning an injection molding machine.
Create colored rubber products with Custom Rubber Corp.
At Custom Rubber Corp. we have two key advantages in molding colored rubber parts: One, we don’t mix rubber or use carbon black and two, we keep our facility immaculately clean.
Companies that mix rubber tend to have carbon black on hand. Carbon black is such a powerful material that keeping just one bag of it in your facility can easily lead to a fine dust of carbon black covering the surrounding area, which can contaminate colored rubber.

Even if you don’t work with carbon black, colored rubber requires a squeaky-clean facility. The second you take a rubber part out of a mold and put it on a dirty or dusty table, that dirt and dust transfers straight onto your nicely colored part.
We regularly service customers in need of molded rubber in colors ranging from red to blue to pink and everything in between. Contact our team today for a quote on your next production run of colored rubber parts.
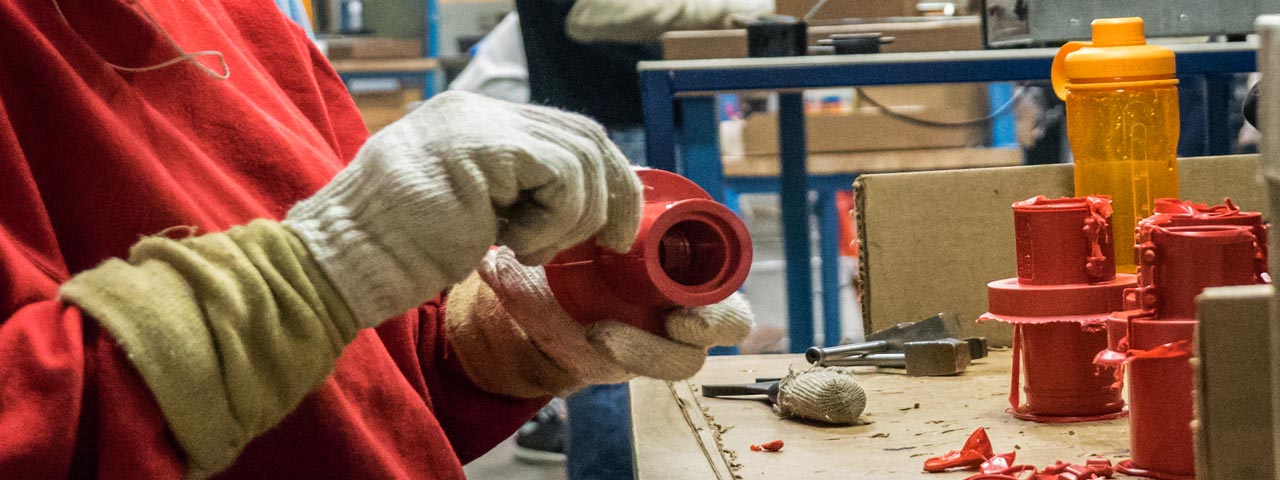
Click here to contact Custom Rubber Corp. for more information on our colorful molded rubber production and design capabilities.