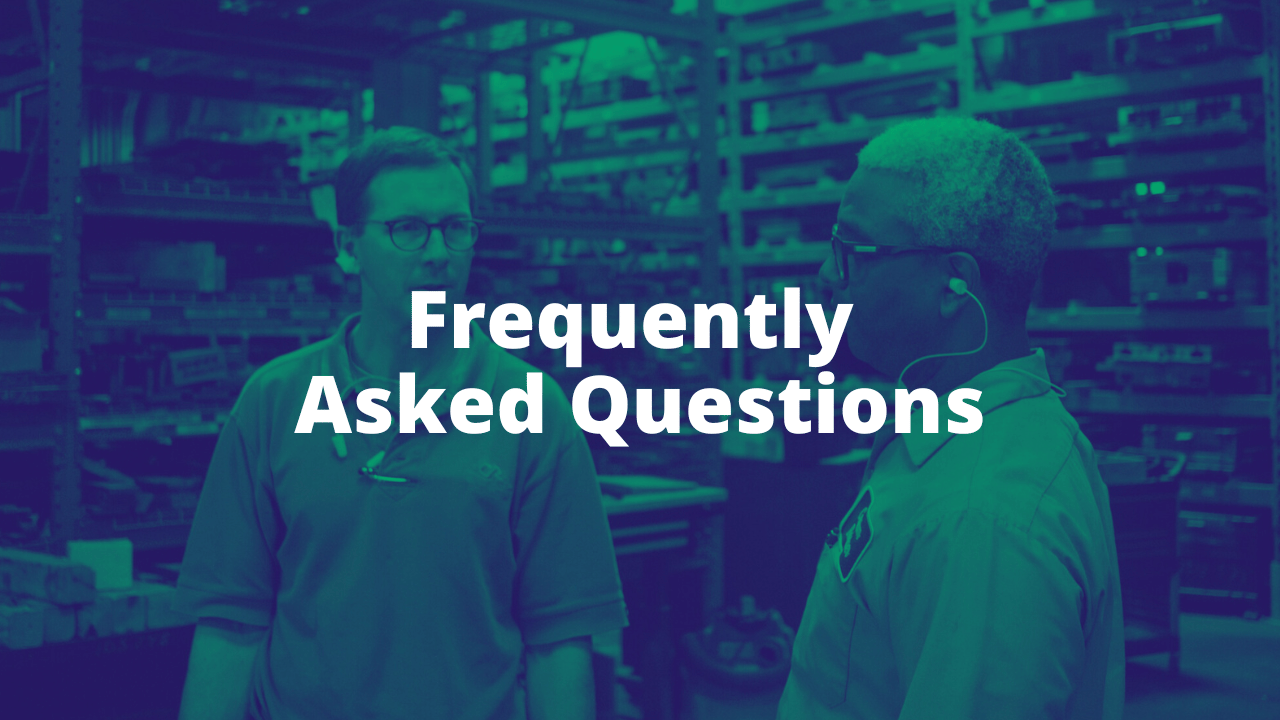
Custom rubber molding is a fascinating and intricate field, playing a crucial role in various industries. This blog post aims to demystify this process by addressing some of the most frequently asked questions, providing insights for those new to this area or considering a custom rubber molding project.
What is Custom Rubber Molding?
Custom rubber molding is the process of shaping rubber into specific products or parts, customized to meet unique specifications. This process is vital in creating parts that fit specific applications, whether in automotive, healthcare, or consumer products.
What Types of Rubber Are Used in Custom Molding?
There are
several types of rubber materials used in custom molding, including natural rubber, synthetic rubbers like SBR and Nitrile, and silicones. Each type has unique properties - for example, natural rubber is known for its elasticity, while silicone excels in high-temperature applications.
What Are the Key Steps in the Custom Rubber Molding Process?
The process typically involves several key steps:
design, where the part is conceptualized;
prototyping, to create a sample;
mold making, the creation of the mold;
production, where the rubber is molded; and
post-production, involving additional finishing or testing.
How Do I Choose the Right Rubber Material for My Project?
Selecting the right material depends on your project's specific needs - consider factors like the environment the part will operate in, exposure to chemicals, and physical stress. Consulting with a knowledgeable manufacturer like Custom Rubber Corp. can guide you in material selection.
What Are the Common Applications of Custom Rubber Molding?
Custom rubber molding finds applications in diverse fields. In automotive, it's used for gaskets and seals; in healthcare, for medical devices; and in electronics, for insulation and protective components, to name a few. You can see many examples of use in different industries on our
industries page.
How Does the Design Process Work in Custom Rubber Molding?
Design in custom rubber molding is a critical phase. It often involves using CAD software to create precise models, ensuring that the final product will function as intended. The design must account for the rubber's behavior during and after the molding process.
What is the Typical Turnaround Time for a Custom Rubber Molding Project?
Turnaround times can vary widely based on the project's complexity and the stages involved. Factors like the complexity of the design, mold preparation, and production volume can influence the timeline. Typically, a 3D printed prototype can be delivered within one to two weeks, while prototype molds generally require two to four weeks. Production molds, however, may take anywhere from eight to twenty weeks to complete.
How Do I Ensure Quality in Custom Rubber Molding?
Quality assurance is vital. Look for manufacturers with certifications and who adhere to industry standards. At Custom Rubber, we're proud to be
ISO Certified, demonstrating our dedication to quality. Consistent quality control measures during production are crucial.
What Are the Cost Factors in Custom Rubber Molding?
Costs in custom rubber molding are influenced by the material chosen, design complexity, mold production, and the volume of parts produced. Understanding these factors can help balance cost with the quality and performance needs of the project. Custom Rubber can help with economical material selection and part design.
What Should I Look for in a Custom Rubber Molding Partner?
When choosing a partner, consider their experience, technical capabilities, customer service, and track record. A good partner should be able to provide guidance throughout the process and deliver high-quality products.
Just call CRC!
Conclusion
Custom rubber molding is a versatile and complex process but understanding its basics, applications, and best practices can demystify it. Whether you’re just exploring the field or ready to start a project, these insights should prove invaluable.