Rubber products are critical in numerous industries, from automotive and medical applications to consumer goods and more. However, like any material, rubber requires regular maintenance and care to preserve its performance and longevity. Without proper attention, rubber components can deteriorate, leading to damage or reduced functionality.
At Custom Rubber Corp., we understand that the lifespan of rubber products depends not only on the materials used but also on how well they’re maintained. By following simple, proactive maintenance steps, rubber products can deliver reliable performance and last longer, helping you avoid unnecessary replacements and costly repairs.
Rubber Products and Their Uses
Rubber products come in many forms and serve a wide variety of functions across industries. Each application relies on the material’s ability to perform reliably under specific conditions. Here are just a few examples:
- Automotive: Rubber is used for seals, bushings, hoses and vibration dampeners—components that must withstand heat, friction and exposure to fluids.
- Medical: Rubber parts provide flexibility and secure sealing for devices and equipment, often requiring precise performance and biocompatibility.
- Consumer goods: From ergonomic grips to protective gaskets, rubber enhances product comfort, safety and durability.
- Industrial equipment: Rubber components absorb shock, reduce vibration and create effective seals in machinery and heavy-duty tools.
- Marine & outdoor applications: Durable rubber resists moisture, UV exposure and harsh environmental conditions.
In every case, the quality of the rubber plays a significant role in both performance and longevity. At Custom Rubber Corp., we use carefully selected compounds tailored to each use case, ensuring durability from the start. But even the highest-quality rubber requires consistent care to preserve its properties and extend its service life.
General Guidelines for Rubber Maintenance
While rubber is known for its durability, everyday environmental factors can gradually cause wear and degradation. Following a few basic maintenance practices can help keep components in optimal condition:
- Keep rubber clean: Dirt, grime and chemical buildup can accelerate the aging process of rubber. Clean rubber parts regularly using mild soap and water. Avoid harsh cleaners, solvents or abrasive tools that could damage the surface.
- Avoid extreme temperatures: Exposure to excessive heat or extreme cold can affect rubber’s flexibility and structural integrity, potentially leading to cracking, hardening or shrinking. Store rubber components in a cool, dry environment and avoid placing them near heat sources or in direct sunlight.
- Protect against ozone exposure: Ozone in the air—especially in industrial settings—can break down rubber at the molecular level, leading to surface cracks and reduced elasticity over time. In ozone-rich environments, apply a rubber conditioner or use products formulated with ozone inhibitors for added protection.
- Regular inspection: Over time, rubber can develop signs of fatigue such as cracking, brittleness or soft spots. Spotting these issues early can help avoid performance failures. Check rubber parts regularly, especially in high-use or mission-critical applications, and replace them if wear becomes visible or function is compromised.
Maintaining Rubber Components in High-Stress Environments
Some rubber components operate under significantly more stress than others, particularly in industries like automotive, transportation and manufacturing. These parts—such as bushings, belts, seals and hoses—are exposed to constant heat, mechanical friction and harsh chemicals that can accelerate wear.
To protect rubber in these demanding conditions, it’s important to take extra precautions. Applying rubber-safe protectants can help shield against thermal breakdown and chemical exposure. Regular inspections are also essential; look for signs like cracking, hardening, soft spots or a noticeable loss of elasticity. If any of these appear, it’s likely time to replace the component to avoid costly failures.
Rubber Storage and Handling
Rubber products can degrade prematurely if they’re not stored and handled correctly. Environmental factors and improper handling techniques can lead to hardening, cracking or loss of elasticity long before a product reaches the end of its expected service life.
Proper storage techniques
Rubber can be highly sensitive to environmental conditions such as light, heat, humidity and ozone exposure. If rubber products are stored improperly, they can lose their flexibility and durability. Direct sunlight, excessive heat or exposure to ozone can lead to cracking and degradation. It’s also important to consider humidity, as excessive moisture can cause rubber to soften or weaken over time.
Tip: Store rubber components in a cool, dry and dark environment—away from direct sunlight, heat sources and ozone-emitting equipment.
Handling with care
The way rubber components are handled during installation, transport or storage is just as important as their storage environment. Rough handling, stretching or exposing the material to contaminants like dirt, oils or solvents can cause permanent damage to the rubber.
Tip: Handle rubber components gently and avoid stretching them unnecessarily. When possible, use clean hands or gloves to prevent oil or dirt from affecting the material.
By paying attention to how rubber parts are stored and handled, you can greatly extend their functional life and reliability.
Signs It’s Time to Replace Rubber Products
Even with regular maintenance, all rubber products will eventually show signs of wear and tear. Recognizing these early indicators can help prevent unexpected failures and ensure continued performance in critical applications.
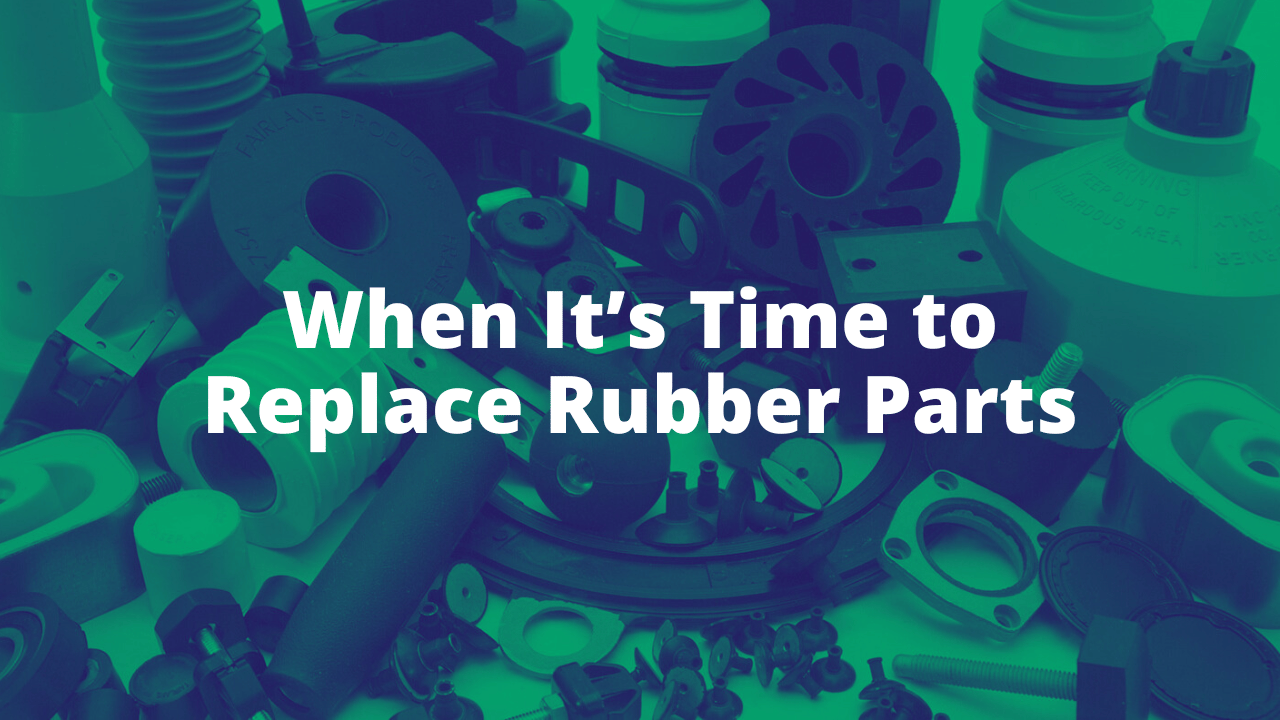
Recognizing wear and tear
As rubber ages or experiences stress, it may exhibit visible signs of damage. Common indicators that it’s time to replace a rubber part include:
- Cracking or splitting: Small fissures or large cracks often appear as the rubber loses flexibility.
- Fading or discoloration: A change in color, especially from prolonged exposure to sunlight or harsh environments, may signal degradation.
- Loss of elasticity: If a rubber component no longer returns to its original shape or feels stiff, it’s likely losing its ability to absorb shock or provide a secure seal.
- Softening or hardening: Rubber that feels either too soft or too hard can no longer effectively perform its intended function.
Damaged or worn-out rubber can significantly affect product performance. In automotive, medical or industrial applications, a compromised rubber part can lead to malfunctioning components, decreased efficiency or even complete failure. For example, a worn gasket might cause leaks, a degraded hose may lead to fluid loss and a cracked seal could result in the failure of an entire system. In mission-critical applications, such issues can cause expensive repairs or safety hazards.
Ensure Longevity and Performance with Custom Rubber Corp.
At Custom Rubber Corp., we understand how vital rubber products are to your operations. If you notice any signs of wear or need replacement parts, we offer custom solutions designed for longevity and reliable performance. Our expert team is ready to help you find or replace rubber products that match your specific needs, ensuring your operations continue without disruption.
Reach out to Custom Rubber Corp. today to explore how our custom rubber solutions can keep your products performing at their best.