Compression molding has stood the test of time as one of the oldest and most dependable methods for producing rubber parts. From its origins in the late 19th century to its continued use today, this process has proven its ability to deliver high-quality, durable components that meet the needs of diverse industries, all while maintaining cost efficiency.
By leveraging the unique behavior of rubber under heat and pressure, compression molding transforms raw materials into solutions that enhance equipment performance, ensure safety and deliver exceptional durability. This enduring process highlights the balance of science and craftsmanship that defines rubber manufacturing today.
A Simple Experiment with Lasting Impact
The origins of compression molding date back to the 1890s when
Harvey Firestone, a key figure in the rubber industry, conducted experiments in his home oven to press and heat rubber into molds. At the time, his goal was to find a way to mold rubber into useful, durable shapes. Firestone’s experiment revealed how the combination of heat, pressure and carefully chosen added chemicals could create strong, functional rubber components. While the process has advanced significantly with modern technology, the basic principles he discovered remain the same.
How Compression Molding Works
Material Behavior Under Pressure
When rubber is placed under pressure and heat in the molding process, it begins to soften and flow, taking on the shape of the mold. The unique properties of rubber, such as its elasticity and ability to withstand stress, are key to this transformation.
As the rubber compound is compressed, it behaves differently based on its formulation. Some compounds might become more rigid, while others maintain flexibility or resistance to abrasion.
The interaction between pressure, temperature and the rubber’s chemical makeup determines the final characteristics of the molded part, such as its hardness, flexibility and durability.
Curing Process & Vulcanization
The curing or vulcanization process is what turns raw rubber into a finished, stable product. During vulcanization, heat is applied to the rubber in the mold, causing the sulfur or other curing agents in the compound to form cross-links between the polymer chains. This chemical reaction solidifies the rubber, giving it strength, elasticity and resilience.
The key to successful vulcanization is carefully controlling the time and temperature to ensure the rubber reaches the perfect balance of hardness and flexibility. Over-curing or under-curing can lead to defects in the final part, which is why precision is critical.
Tooling and Mold Design Considerations
The success of compression molding depends heavily on the quality of the mold.
Tooling needs to be precise and well-maintained to produce high-quality parts, especially when dealing with intricate designs or tight tolerances.
At Custom Rubber Corp., we specialize in both taking over
existing tooling and developing new molds that meet specific customer requirements. The process involves meticulous planning and design to ensure the molds are durable, efficient and capable of consistently producing parts that meet exact specifications.
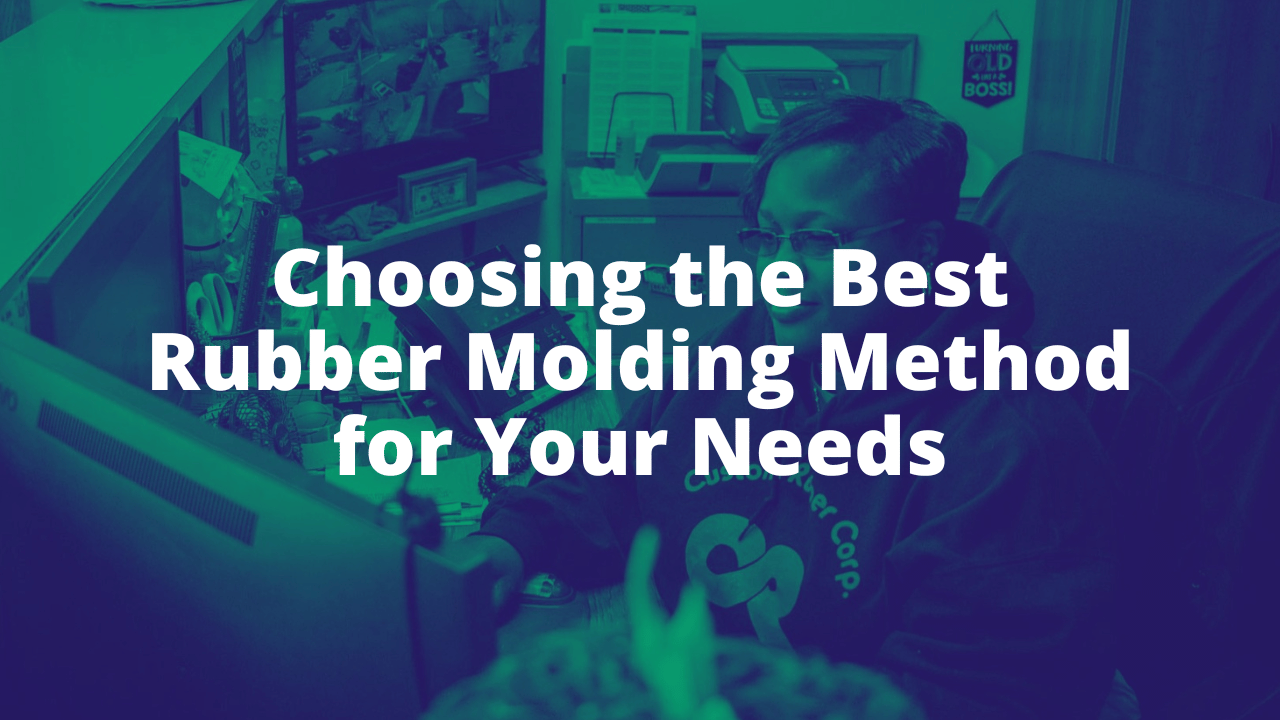
When Compression Molding is the Right Choice
Low to Medium-Volume Runs
Compression molding is an excellent choice when production demands are moderate. It is cost-effective for low to medium-volume runs, especially when tooling is already available. This makes it ideal for industries that need smaller quantities of parts, whether for prototyping, limited production runs or specialty orders.
Large, Simple Parts
When it comes to large rubber parts, compression molding often has the upper hand over methods like injection molding. Large parts typically require longer curing times, and compression molding’s straightforward process is better suited for handling those extended cycles.
For example, when producing sizable gaskets, seals or bumpers that don’t require complex geometries, compression molding ensures both quality and efficiency without the need for highly specialized injection equipment. In addition, compression molding equipment is a smaller investment when compared to injection molding machines.
Advancements in Compression Molding
While much about compression molding is the same as it was in the early 1900s, there have been some advancements. On the chemistry side, there are new additions and ingredients that have enhanced both the physical properties of rubber and the efficiency of the manufacturing process far beyond what was possible a century ago.
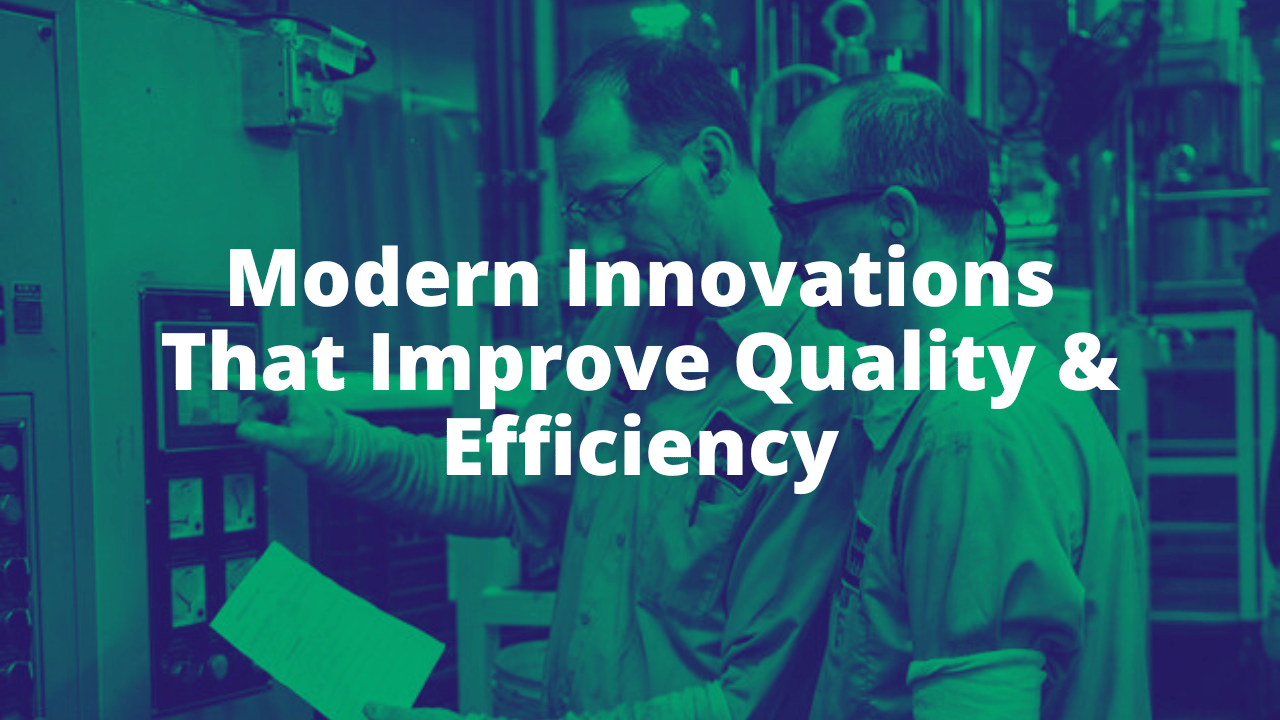
Even more significant, the addition of vacuum boxes on compression molding equipment has revolutionized the quality level and productivity possible with compression molding. Precise computer PLC controls for pressure, closing speeds and curing times has further optimized molding capacity.
All of CRC’s compression molding machines are modern, offering vacuum boxes as well as advanced PLC controls. With these innovations at our disposal, there's no reason not to leverage the benefits of modern compression molding equipment to meet your production needs.
Common Applications of Compression-Molded Rubber Parts
Compression molding plays a key role in producing protective components such as bumpers, seals and gaskets. These parts are crucial in safeguarding equipment from damage, reducing wear and tear and preventing leaks in a wide range of industries.
For example, industrial seals used in hydraulic systems ensure that pressurized fluids stay contained, reducing the risk of leaks that could compromise machinery and create safety hazards. Rubber bumpers, often used in shipping, help prevent damage to goods or equipment by absorbing impacts and providing a protective barrier during transportation.
Whether it’s aerospace fuel plugs or heavy-duty rubber pads for construction machinery, compression molding provides high-performance solutions that help protect both people and equipment.
Customized Solutions for Every Industry
The flexibility of compression molding makes it an ideal method for creating parts with customized features for specific industries. Color-coded rubber bumpers and pads are frequently used to help with identification or to denote different material types, providing quick visual cues to workers. Non-marking rubber parts are used in environments where they must not leave marks or scuffing on surfaces, like in delicate industries such as electronics or high-end manufacturing. For industries that require precise, tailored components, compression molding offers the versatility needed to design rubber products that meet specialized requirements.
Custom Rubber Corp. for Your Compression Molding Needs
With over six decades of expertise in compression molding, Custom Rubber Corp. has become a trusted partner for industries seeking durable and high-performance rubber parts. Known for taking on custom projects that other companies might hesitate to pursue, we pride ourselves on our ability to tackle even the most challenging molding requirements.
From automotive to medical applications, we bring expertise and innovation to every project, ensuring that we meet the specific needs of each industry we serve. Whether compression molding is the best option or another rubber solution is more appropriate, we work with you to find the most efficient and cost-effective approach.
Want to learn more about how we can help your business?
Contact Custom Rubber Corp. to discuss your next project.