At Custom Rubber Corp., we’ve spent decades providing high-quality molded rubber solutions, building a reputation for responsiveness and customer satisfaction, from Design to Delivery. Our commitment to meeting your unique needs means we offer a variety of molding techniques to ensure the best outcome for your projects.
Transfer molding is a versatile and efficient technique that excels in producing precision rubber parts across a range of industries. Whether you need intricate geometries or rubber-to-metal bonding, transfer molding can offer significant advantages.
Understanding different molding techniques is crucial for making informed decisions. By knowing what transfer molding offers and how it compares to other methods, you’ll be better equipped to choose the right process for your custom rubber components.
What is Transfer Molding?
Transfer molding is a rubber molding process that combines the precision of injection molding with some of the simplicity of compression molding. In transfer molding, raw rubber material, which is often called a preform, is placed into a chamber known as a “pot.” A plunger then applies pressure, forcing the rubber through a channel and into the mold cavity where it takes the shape of the final part. Heat and pressure are applied to vulcanize (or cure) the rubber, ensuring it solidifies with the desired characteristics.
Compared to compression molding, where rubber is shaped by being pressed directly into the mold cavity, transfer molding allows for more intricate designs and tighter tolerances. It also offers better control over material flow, reducing defects and inconsistencies. While injection molding injects rubber directly into a closed mold at high pressure, transfer molding is more efficient for projects involving metal inserts or requiring medium production volumes. Transfer molding also works well with parts molded with colored rubber other than black.
Key Advantages of Transfer Molding
When your project demands intricate designs and consistent results, transfer molding stands out for its ability to produce complex geometries with precision. The process controls how rubber flows into the mold cavity, ensuring detailed features and tight tolerances are consistently achieved. This makes transfer molding ideal for parts where accuracy is non-negotiable, such as seals, gaskets or components with embedded inserts.
Transfer molding minimizes flash, which is the excess material that can form along parting lines in other molding methods. With less flash to trim, post-processing time is reduced, resulting in faster delivery of clean, finished parts.
Transfer molding is also valuable in rubber-to-metal bonding, seamlessly molding rubber around metal inserts like brass, aluminum or steel. This capability is invaluable for industries that rely on durable, bonded components, such as automotive and electronics.
Applications of Transfer Molding
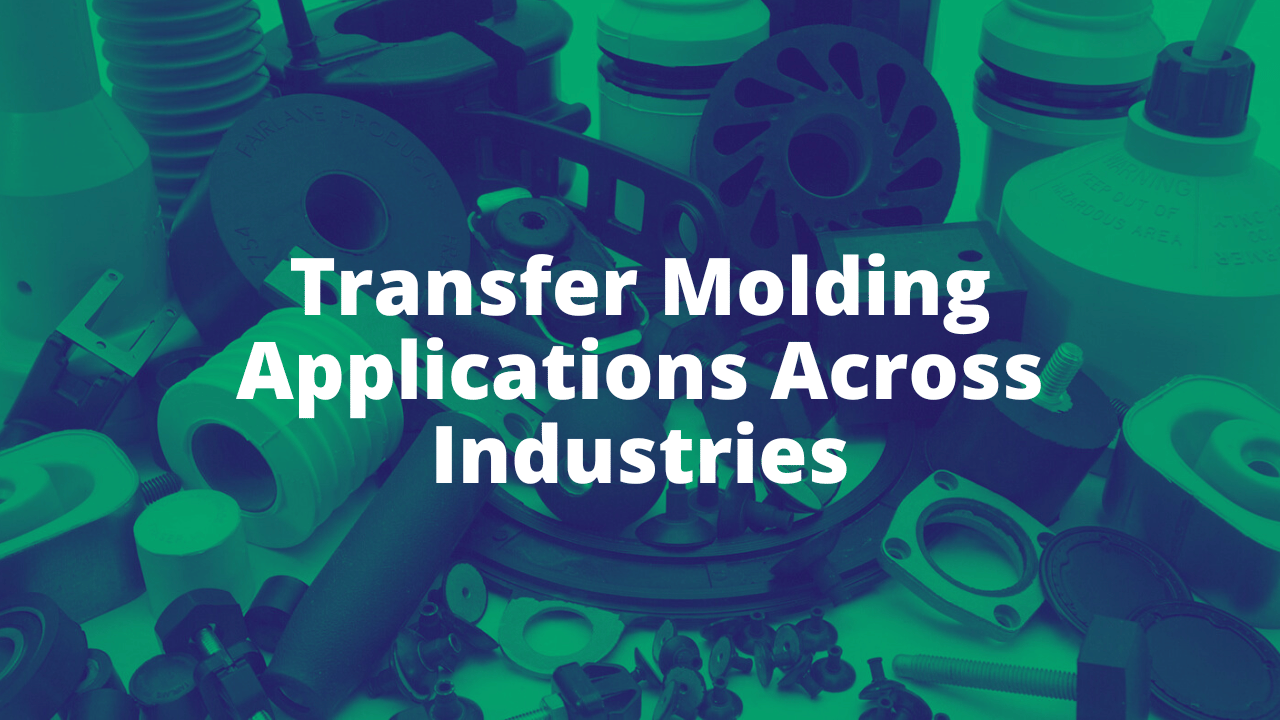
Transfer molding is widely used across industries that require high precision, durability and performance. It’s the preferred method for parts that demand complex geometries and tight tolerances. Here are some of the key applications where transfer molding stands out:
-
Automotive Components: Used for manufacturing precise seals, gaskets, bushings and vibration-damping parts, ensuring reliable performance in high-stress environments.
-
Electronics: Ideal for creating rubber-encased connectors, insulators and components that protect sensitive electronic parts from moisture, dust and other environmental factors.
-
Medical Devices: Perfect for producing precision parts like seals, diaphragms and gaskets that meet rigorous cleanliness and performance standards.
-
Marine and Industrial Applications: Ensures the production of durable, bonded parts designed to withstand the challenges of harsh environments, such as saltwater and extreme temperatures.
Transfer Molding Process Breakdown
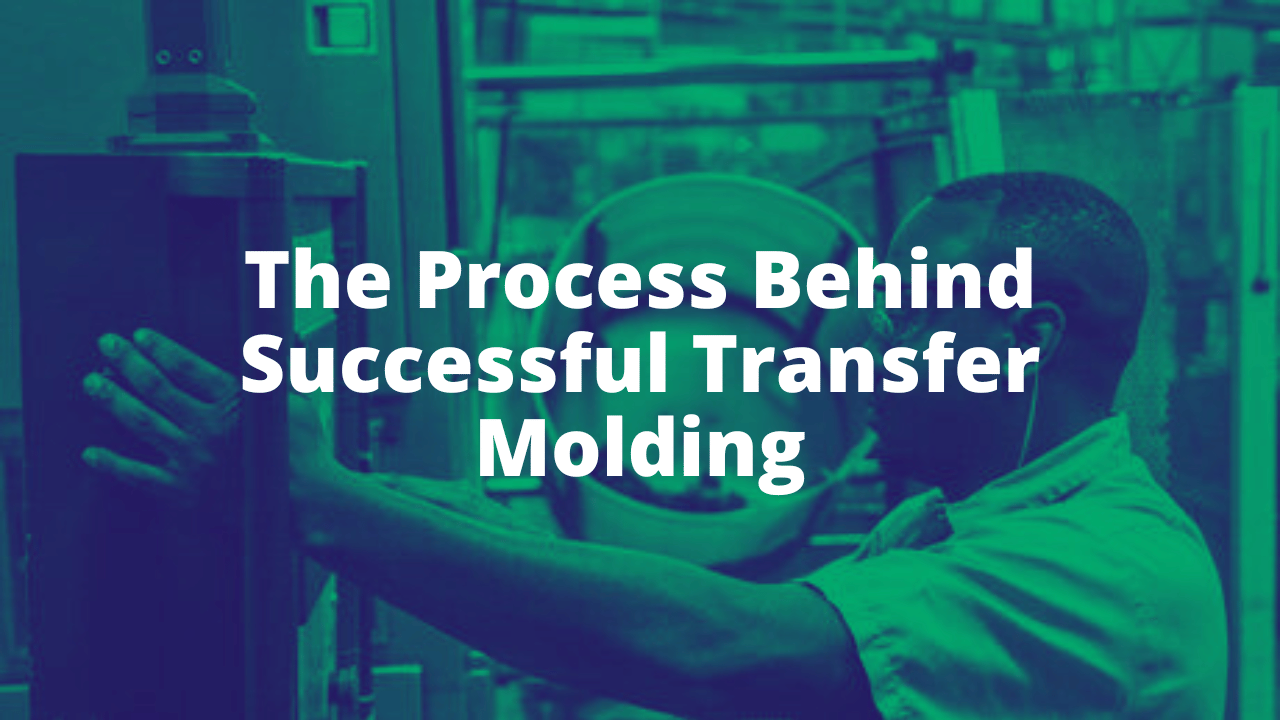
1. Preparation
The process begins with the design and creation of the mold. Custom Rubber Corp. works closely with customers to develop a mold that meets the precise requirements for the final part. The design must take into account part dimensions, material flow and any embedded features, ensuring the mold will yield high-quality results every time.
2. Material Placement
Next, the pre-measured rubber material is loaded into the transfer pot. The rubber material is carefully chosen based on the specific requirements of the application, such as hardness, flexibility or temperature resistance. This ensures the right material properties are achieved in the final part.
3. Applying Pressure
Once the rubber is placed in the pot, a plunger applies pressure to force the material into the mold cavity. The pressure ensures that the rubber fills every intricate detail of the mold, allowing for the creation of complex shapes and precise features. This step is key to achieving consistency and accuracy in each part.
4. Curing
Heat and pressure are applied to the rubber as it cures, or vulcanizes, in the mold. The curing process ensures that the rubber solidifies and gains its desired physical properties, such as elasticity and strength. This is when the raw rubber transforms into a finished, durable part that meets specific performance standards.
5. Cooling and Demolding
Once the rubber has cured and allowed to cool, the finished part is carefully removed from the mold. The part is now ready for post-processing or packaging, depending on the requirements. This step marks the completion of the transfer molding process, where the part is fully shaped and hardened.
Tooling Considerations
Precise tooling is critical in transfer molding to achieve consistent, high-quality results. The mold design must be accurate, and the tooling must be robust enough to handle the pressure and heat involved in the process. Custom Rubber Corp.’s expertise in tooling ensures that every mold is engineered for optimal performance. With our experience in both creating new molds and transferring existing tooling, we can minimize downtime and support smooth production runs.
Quality Control
At Custom Rubber Corp., quality control is an integral part of our transfer molding process. Every part undergoes comprehensive inspections to verify its dimensions, functionality and durability before it leaves our facility. Our team follows strict guidelines to check for common defects like non-fills, flash or inconsistent material flow. We also conduct performance tests to ensure that each part is capable of withstanding the demands of its specific application when necessary.
Is Transfer Molding Right for Your Project?
Transfer molding is the ideal choice when you need complex, detailed parts that require precise tolerances and may include embedded components like metal inserts. This method is particularly effective in medium production volumes and colored rubber, offering the consistency and quality required for critical applications in various industries.
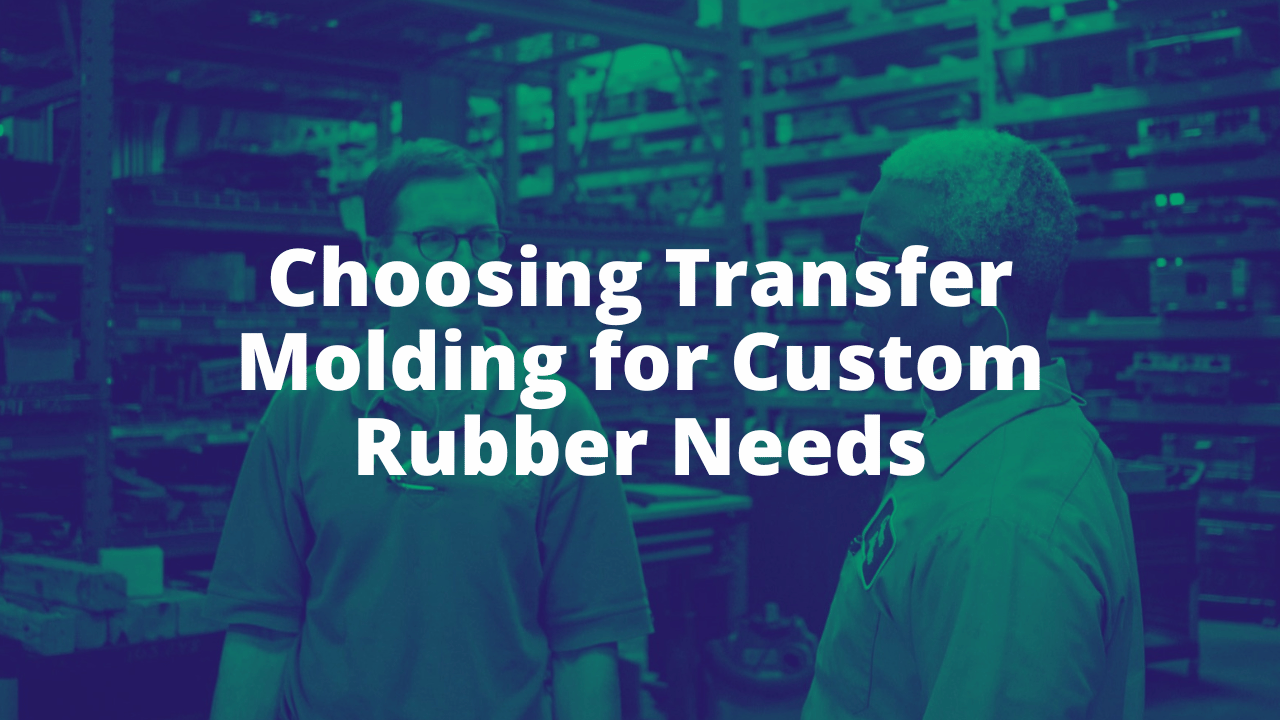
However, transfer molding may not always be the best choice for every project. If your part design is simpler,
compression molding might be a more cost-effective option. For projects that require high-volume, large-scale production,
injection molding can provide faster production speeds and greater efficiency for large quantities, making it preferred for mass production runs.
Not sure which process is best for your needs? Custom Rubber Corp. offers expert consultation services to help you evaluate your project and select the right molding technique for your specific application.
Contact our team today to learn more about our rubber solutions!